In search of 'rare earths'
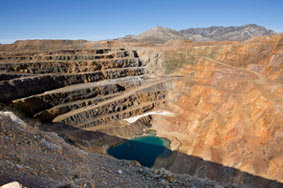
Undermining China's Monopoly on Rare Earth Elements
Full operations will start at a U.S. mine by the end of next year.
By Katherine BourzacTechnology Review
December 22, 2010
Molycorp has secured the permits and funding needed to restart production at a mine in Mountain Pass, California, that would become the first U.S. source of rare earth elements in more than a decade. The mine is one of the world's richest deposits of these elements, which are critical for making components found in a wide range of technologies. On Tuesday, the company announced that it will partner with Hitachi Metals of Japan to turn materials from the mine into high-strength magnets, which are vital in electric vehicles, wind turbines, and many other products.
China currently has a lock on the market for rare earth materials: in 2009 it provided 95 percent of the world's supply, or 120,000 tons. This concentration of supply has become a major issue in recent months, particularly after China temporarily blocked exports of these materials to Japan in September. A Critical Materials Strategy document issued by the U.S. Department of Energy last week points to the "risk of supply disruption" in the short term. Worldwide demand for rare earth elements was 125,000 tons in 2010 and is expected to rise to 225,000 tons by 2015.
The mine is a 50-acre open pit about 50 miles outside Las Vegas, surrounded by a stark landscape of red-brown mountains, Joshua trees, and the occasional cactus. Molycorp has begun draining groundwater that seeps into the bottom of the pit and removing areas of rock called "overburden" to expose a layer of bastnäsite, a mineral rich in rare earth elements. Expansion of operations will push the mine from a depth of 500 feet to 1,000 feet in the coming years.
By 2012, the revamped U.S. mine is expected to produce around 20,000 tons of rare earth materials per year. Molycorp plans to use new processing techniques that it claims are more environmentally friendly and less expensive than conventional methods.
The Mountain Pass mine used to be the world's biggest supplier of rare earth elements, but it closed in 2004, after a 1998 wastewater leak and the arrival of Chinese suppliers that offered lower prices. (One reason for the lower prices is that nearly half the rare earths produced in China are made as a by-product of iron mining.)
Molycorp expects to sell about 3,000 tons of rare earths this year, produced from ore stockpiled before the mine was closed. It is also gearing up for active mining, with financial support from an initial public offering this summer and recent investment from Japanese firm Sumimoto.
The company's total projected production could meet the current demand for rare earths in the United States. Molycorp has not disclosed who its customers will be, but CEO Mark Smith said on a tour of the mine last week that it has inked contracts to sell 25 percent of the 20,000 tons of material it expects to produce during the first year of full-scale operations, in 2012, and has letters of intent to sell the rest. "We're focused on the U.S., Japanese, and European markets," he said.
Under current permits, the company could potentially double production, to 40,000 tons a year, beyond 2012. Smith says demand is likely to exceed supply for some years to come, even if Lynas Corporation's Mount Weld mine outside Perth, Australia, begins production as expected in summer 2011. That company expects to produce 15,000 tons of rare earth elements a year by 2015.
Even with raw materials in place, U.S. manufacturers can't produce many important technologies based on rare earth elements. Bastnäsite from the Mountain Pass mine can be processed on site to make didymium oxide, a powder that contains the element neodymium, which is critical for making lightweight permanent magnets. But didymium oxide requires further processing to make the neodymium-iron-boron alloy from which the magnets are made. The magnets found in a wind turbine require several hundred kilograms of neodymium.
No company in the United States currently has the technological capacity, or the necessary intellectual-property licenses, to make neodymium magnets. Yesterday, Molycorp and Hitachi metals announced an agreement to produce these magnets in the United States; the two companies plan to sign a definite agreement by April 2011. According to the DOE, only 10 companies, which are located in Germany, Japan, and China, are currently licensed to make such magnets. The intellectual property is owned by Hitachi Metals and by Magnequench, which is now part of AMR Technologies, a company based in Canada that was bought by a Chinese consortium in 1995. Molycorp's Smith says that producing alloys for magnets could increase the company's profit margins by 125 percent.
A recent report published by the U.S. Geological Survey estimates the total rare earth reserves in the United States at 1.5 million tons. But the report says it's unclear how much of these reserves can be mined economically. The DOE report outlines a strategy of diversifying the international supply of rare earths, identifying substitute materials, and finding ways to use the materials more efficiently and recycle them. Researchers at Hitachi, GE, and the University of Delaware are collaborating on the development of an alternative magnet material that requires smaller amounts of rare earth materials, or none at all. But this and similar projects are still in the early stages.
Copyright Technology Review 2010.
0 Comments:
Post a Comment
<< Home